The use of gold plating in the electronics industry has been an ongoing part of the expansion of more complex digital electronics and equipment throughout many industry sectors. According to BullionStreet, over 320 tons of gold are used each year in the electronics industry. This includes gold in PCs, mobile phones, tablets and other devices. The overall use of gold in electronics is via gold plating. Gold plating is primarily used on contacts for switches, relays, and connectors
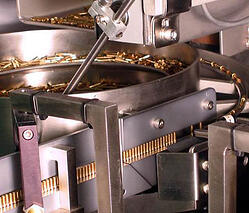
Gold has the combined elements of electrical conductivity, ductility, and doesn’t corrode at high or low temperatures. The corrosion resistance of gold is one of the key factors that it is used for in electronics. According to GoldAvenue, gold’s resistance to corrosion offers “atomically clean metal surface which has an electrical contact resistance close to zero, while its high thermal conductivity ensures rapid dissipation of heat when gold is used for contacts.”
Several guidelines have been established by AMP Incorporated for the use of gold plating in electrical contacts. Below is a summary of some of these guidelines.
High Reliability Applications and Gold Plating – For connector applications in electronics that require reliability, it is important for the separable contact interface to be shielded from environmental deterioration. An application of gold onto the interface of a separable connector provides a long, stable and very low contact resistance for the component.
Corrosive Environments and Gold Plating – Corrosive environments such as high humidity locations or an environment that contains corrosive pollutants like chlorine or sulfur gases will attack and degrade metals like nickel. This corrosion will interfere with electrical contact. Gold doesn’t break down in these conditions. However, if the gold plating is too thin or porous, it will break up, so it is important for the plating to be done at the correct thickness for full protection and with a suitable under layer metal.
Suitable Under Layer Metals for Gold Plating –In order to avoid degradation of gold plating, especially in corrosive environments as mentioned above, gold plating should be applied over an under layer of a quality metal like nickel. An under layer of nickel will act as the following for a gold plated surface:
- Pore-Corrosion Inhibitor – Nickel as an underplate prevents corrosion via pores in thin areas of gold plating.
- Corrosion Creep Inhibitor – Provides a barrier against corrosion
- Diffusion Barrier – Prevents diffusion of other metals like copper or zinc into the gold surface.
- Mechanically Supporting Under Layer for Contacting Surfaces – Nickel increases gold plating’s durability.
Thickness of Gold Plating Based on Requirements of Electronic Component – The determination of the correct gold plating thickness depends on the application of the electronic component. Despite the decline in the price of gold in recent months, keeping the plating thickness as low as feasible is a good place to begin when determining the overall thickness of the plating. According to the AMP report, “In general, a 0.8 micron (30 micro inches) coating of hard gold over a minimum of 1.3 microns (50 micro inches) of nickel gives a degree of durability considered adequate for most connector applications. Thin coatings of 0.03 - 0.1 microns (1 - 4 micro inches) of hard or soft gold over nickel underplate should be used only for applications in which the risk of fretting is minimal. Increasing the thickness of a gold coating tends to decrease the porosity which reduces the contacts’ vulnerability to pore corrosion.
Gold Plated Contacts Effective at High Temperatures – With gold’s properties, it is an effective protection for electronic contacts exposed to high temperatures (>125⁰C/>257°F). To be certain of protection against elevated temperatures, the nominal gold and nickel thickness should be increased.
These are just a few guidelines for the use of gold plating in electronics. Each application of the electronic component that is to be plated should be determined to make certain that all factors are considered and planned for prior to plating in order to obtain the target performance.