Electroplating is a process whereby one metal is plated onto another via an electrodeposition method. Customers seek out electroplating for their parts for many reasons such as aesthetics, corrosion protection, increased hardness, wear resistance, increased conductivity, and decreased friction. It allows manufacturers to use base metals that are less expensive and apply a high quality coating to them to achieve the certain desired properties on the finished part.
Electroplating requires the use of a DC power supply to transfer electrons to the substrate. The transfer of electrons to the substrate creates the energy which is required for the deposition of positively charged metal ions in the plating bath solution onto the now negatively charged substrate. The relationship among the amount of metal plated and the transfer of electrons may further be explored by researching Faraday’s Law.
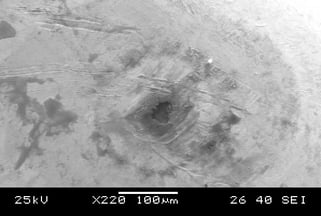
Electroplating is the deposition of a metal onto a surface, but “corrosion is defined as the destructive and unintentional attack of a metal; it is electrochemical and ordinarily begins at the surface (Callister, 2007).” Corrosion is often times seen as the process opposing electroplating because it involves the transfer of electrons in the opposite direction. The corrosion process does not require an input charge or power supply. The first step in a corrosive reaction is the loss of electrons from the substrate. Depending on the corrosive environment, these electrons are accepted by a positively charged ion most likely in solution and the metal is left with a positive charge. The corrosion process may further be studied by researching the Nerst equation.
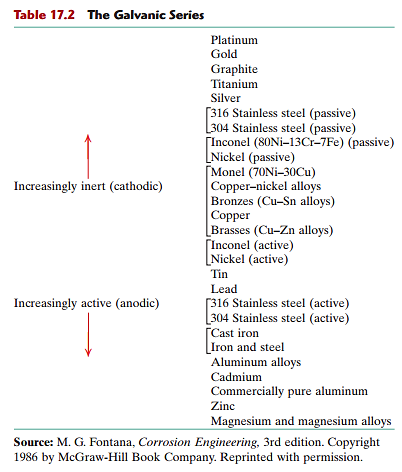
Once the corrosion process begins, and is untreated, the function and material properties of the part become highly compromised. The properties of a material determine how easily it will become corroded in certain environments. Typically, inert or cathodic materials will be much more resistant to corrosion than anodic materials (see table 17.2 for a list). This is logical as an anodic material will more readily give up electrons –starting the corrosion process. Ultimately the environmental conditions will have the greatest impact on the corrosion rate.
Electroplating a metal is a method of reducing the corrosion rate. In general, for electroplating to provide superior corrosion resistance, a metal which is more inert than the base material should be chosen. In addition, thicker deposits and tighter grain structures will result in enhanced resistance to corrosion. A surface finish which is less porous will prevent oxidation and subsurface galvanic migration. Coatings can be applied to give adequate protection to various substrates.
We offer several different types of electroplating processes, as well as several different finishes, including gold, silver, nickel, copper, Tri-M3TM (Tri-Alloy), electroless nickel, electrolytic nickel and passivation. At Electro-Spec we are committed to providing quality service for all your finishing needs. Contact us today to see how Electro-Spec can help you on your next project.
Information and Table compiled from:
Callister, W. (2007). Corrosion and Degradation of Materials. In Materials science and engineering: An introduction (7th ed., pp. 643-644). New York: John Wiley & Sons.