Given the importance of the plating process and the value of the material being used, it would be logical to assume that parts would be designed for the most efficient and effective electroplating possible. Unfortunately due to intricate engineering designs and micro miniature components, it is not always feasible to have a “plating friendly” part.
Electroplating, along with other finishing options, take their place at the end of the manufacturing process. It is incumbent on all parties, including the plater to work together in order to provide the best component possible.
Additionally, sometimes a part’s design will necessitate a difficult structure for applying even finishing, whether it’s electroplating or a more traditional finishing method. There are a myriad of reasons why parts are created with geometries that make them difficult to electroplate.
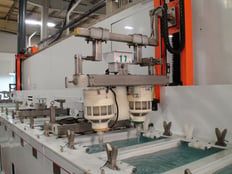
Parts with difficult geometries pose numerous challenges during the electroplating process. Rack or wire plating present challenges all to themselves. Parts are fixtured on splines or wire, which if not done correctly can lead to an air pocket. An air pocket will not allow for solution turnover in that area and consequently no plating.
Another issue to consider is complex or intricate Inside Diameters (ID’s). This can mean; an ID with multiple steps, an ID that is long, or dead holes. These surfaces can prevent drainage for proper rinsing, trapping solution and preventing even finishing. The process of electroplating parts with difficult geometries creates overall challenges in plating distribution.
It is impossible for engineers and designers to always create parts that are easy to electroplate; what’s needed is a plating company that is always working to find a better way to plate customer’s components. At Electro-Spec, we are always on the cutting edge of innovation in mechanical and chemical improvements to electroplating. Spouted Bed Electrode (SBE) Plating is one such innovation we are proud to be a part of. This process has been specifically designed for flat parts, small parts, parts with tabs, counter bores, difficult geometries, and nesting parts. It is the perfect solution for plating where conventional barrel and vibratory plating methods are not practical or possible.
A chamber with ultrasonic action is used to perform the SBE process; we pump a continuous flow of solution into and out of this chamber. This process provides fresh plating electrolyte while facilitating part movement throughout the electroplating process. This continuous flow of solution is also utilized in the rinsing of the parts to ensure all plating solutions and salts are removed from the parts before drying.
The result of SBE plating is that each part subjected to this process receives very uniform plating coverage. All low and high density areas, counter bores, and complex shapes are plated without interruption or variation in deposits.
When customers are using high quality and expensive materials to protect against corrosion and other difficulties, it makes sense to use a process that provides the best opportunity to for full coverage. Our SBE plating services, along with a host of other high tech plating and finishing options, help clients from various industries maintain the highest quality and integrity when finishing parts.
To learn more about our innovation, please contact us directly. We’ll be happy to discuss your project or component and together we will produce the best value added component possible.