Thanks to its unique advantages over other plating processes, electroplating is used in a number of different applications today. Electroplating is a process in which a layer of metal is applied to the surface of another to create an attractive or protective coating. It was discovered in 1805 by Italian chemist and professor Luigi Brugnatelli who, like many great inventors, stumbled upon the process accidentally.
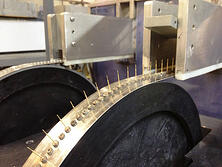
Brugnatelli discovered electroplating while conducting a series of experiments using voltaic electricity, a discovery made just a few years earlier by Brugnatelli’s friend and colleague, Allissandro Volta. Brugnatelli’s first electroplating success is documented in a letter that he wrote to the Belgian Journal of Physics and Chemistry, in which he explains how he was able to “gilt in a complete manner two large silver medals, by bringing them into communication by means of a steel wire, with a negative pole of a voltaic pile, and keeping them one after the other immersed in ammoniuret of gold newly made and well saturated.” This is the process that we now know today as electroplating.
An object is electroplated by connecting it to the negative terminal of an electric battery or other source of direct current to create a cathode. The positive terminal is connected to a metal bar that serves as an anode. These components are submerged in an electrolytic bath composed of a solution containing a salt of the metal that forms the coating. When a current is applied with the battery, electrolysis creates a coating on the cathode. The longer the process continues, the thicker the coating.
Before electroplating was discovered, two main processes were used to plate metals onto other metals. The first, called “water gilding,” was used to coat inexpensive objects with a very thin flash of gold. To obtain a thicker plate of gold, a second method called “fire gilding” was used. This method involved the use of a mercury mixture, and was thus very dangerous. Both plating processes were less than ideal for common use.
Despite Brugnatelli’s breakthrough in a plating process that was both safe and effective, his invention was largely unknown. Brugnatelli’s differences with the French Academy of Sciences, which was the leading scientific body of Europe, prevented his discovery from being published and shared with the rest of the scientific community. It was only until decades later, in 1839, that the process was developed independently by scientists in Great Britain and Russia. Just a year later, it was refined and patented by Henry and George Elkington of England.
The popularity of electroplated items that ensued was a result of many different factors. Electroplating was an inexpensive and safe way to enjoy the beauty of gold and silver. It was therefore extensively used to add decorative elements to objects both large and small. In Russia, for example, cathedral domes and religious statues were electroplated with gold. Smaller items, such as copper vases and coins were also gilded with gold and silver using this method.
Another benefit of electroplating, compared to the other plating techniques from that time, was that it offered corrosion and wear resistance. Electroplating allowed metalworkers to achieve a thick coating of metal over the desired object, though generally no more than 0.002-inches thick. Unlike items that were plated using the water gilding process, electroplated objects offered a sufficient barrier against corrosive environmental conditions. Electroplated parts thus performed better and lasted longer than items without protective plating.
The advantages of electroplating made it a success in the 19th century, and it soon became the preferred method of plating. While it was continuously refined to produce more consistent and high-quality results, the electroplating process did not experience any further technological breakthroughs until the 20th century, which marks the development of the electronics industry. Electroplating provided a corrosion-resistant and electrically conductive layer for electronic components such as circuit boards and connectors. These were usually plated with gold. The surge in electroplating raised concerns over its safety and, by the mid-1950s, the cyanide plating baths were largely replaced by acid formulas more suited for large-scale commercial use.
A number of industries rely on the electroplating process to add both functionality and decorative finishes on objects small and large. Today, it’s commonly used in the electronics industry to enhance the performance and longevity of electrical components, but it has had a long history of use in the architectural and metalworking industries. Electroplating is responsible for gilding large religious structures, and providing an attractive finish to decorative vases and medals. It is an enduring chemical process that promises to find many more applications in the future.